Construction
Some manufacturing issues that could become a reality would be the use of the plasma table provided by the university. The mounting tabs for the hydraulic cylinders and the joints will need to be CNC cut. Lack of experience with this machine could cause an issue. To solve this problem, a staff technician will aid in the manufacturing of these parts.
The plasma cutter might also cause issues later in manufacturing due to the precision of the machine. Although it makes straight lines, the size of the part is affected during the cutting due to the arc of the plasma.
This was investigated more once the brackets and hinges are in the welding state.
During the manufacturing of the device, the issues that were projected did come into affect. The major issue was the holes on the brackets. These holes although programmed for one inch, they were cut slightly larger. This became an issue during the final assembly once the bolts were inserted. The extra clearance created some un-wanted movement during operation. To fix this problem, the holes should be offset roughly .030 inch inside the hole. This would allow for the arc blowout during the cutting process.
The device itself will be built at SOF Farms. The booms will be retrofitted to an existing 3-point sprayer unit. All but the hydraulic rams will be manufactured in house. This project is made of two hydraulic rams and two 10-foot boom assemblies. The first part that will be constructed will be the booms. Each boom will consist of two 10-foot, 1 ¼” X 1 ¼” square tubing braced down the center. This will require the use of a horizontal band saw to ensure good straight cuts. The hydraulic brackets and the hinges will be cut at the CWU fabrication facility with the plasma table. Once these are cut they will be attached to the booms. The booms, hinges and brackets will require welding, which will also be done at the SOF shop.
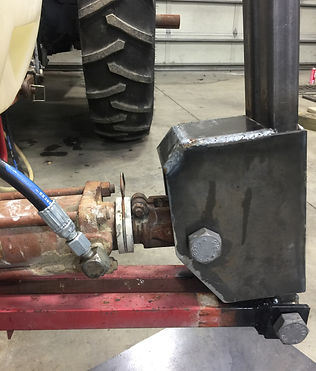

Manufacturing issues
Conception
To bring my idea and design to life, I used solidworks 3D software to create the parts and a complete assembly rendering. Using this software allows you to make sure the device functions properly before actually manufacting it. The other benefit of using this type of software is that you will have the exact size and weight of the parts needed. This allows one to plan ahead when ordering parts and to not having the issues of ordering to much or to less.
